The cause drain pump does not turn on. Preventive measures and regular maintenance. Malfunctions and ways of their elimination
A) Pump starter does not work
Before analyzing the reasons for the drop in water flow in the hydraulic circuit, it seems useful to consider the most obvious malfunction: the pump starter does not work.
The electroscheme of most pumps is quite simple. On small pumps with a single-phase drive motor, even starters are sometimes absent: the engine is started with a conventional starting capacitor (PSC circuit, see section 53).
For large pumps, three-phase current motors are used and the application of the starter becomes necessary. On the circuit diagrams, the "start-stop" button, the fuse (thermal relay) and finally the coil of the starter "Pump of ice water" (PEG).
If the actuator does not work, the defect is detected relatively easily and quickly (see Section 54). It remains only to determine why this or that safety device has worked, to fix the malfunction and to try to make it so that the defect no longer repeats.
B) The starter is closed, the pump "buzzes", but does not start
The three-phase motor starter has tripped. The engine starts to "buzz", but does not rotate. There can be several reasons: either the pump has jammed, or the problem is in the engine itself, or the voltage on one of the phases in the mains has disappeared. In the latter case, the fuse (thermal protection relay) very quickly cuts off the voltage, otherwise the engine will have a high probability of "giving the soul to God".
In order to detect a phase failure or so-called "phase skew," press the "Stop" button and check the voltage for each of the phases at the input terminals. Never check the voltage at each phase with respect to the neutral wire (if the two phases are the same, then you will not be able to detect anything!). Check the voltage between phases L1-L2, L1-L3 and L2-L3. All voltages must have the same value. Otherwise, the cause of the malfunction is in the power supply.
If the voltages of all three phases are normal, check that they are present at the input of the fuse box (key 2). If there is no voltage at any phase, either the wire is broken or the connection is poor. Similarly, check the output voltage from the fuse box (key 3). Here the problem can be either in the fuse blown, or in the fault of the disconnector (bad contact). These faults are discussed in detail in Section 55.
Finally, check the voltage at the input of the starter (key 4). Here is the same:
either the wire is broken or the terminals are tightly clamped.
If the voltage is normal at the input of the starter (item 4), before starting further checks, disconnect the motor winding from the terminals pos. 7 at the output of the starter.
Disconnect the motor winding from the terminal box (key 7 in figure 92.3), then close the pump switch (key 1) to activate the starter. In this case, since the motor winding is disconnected from the starter and the starter has tripped, a voltage must appear on the terminals (key 7).
If this does not happen, check the voltage at the terminals (item 5 in figure 92.2) to identify possible problems in the terminal box, on the connecting wires between the starter and the terminal box, as well as in the power circuit of the fuses or the starter.
If there is voltage on the terminals (key 7), the fault is caused either by the breakage of the connecting wires between the motor and the terminal box or by the motor itself (see section 62. and also section 53) or by the fact that the pump does not allow the motor to rotate (because, for example, it completely jammed).
If the drive motor of the pump is a single-phase motor with a starting winding, and this engine "buzzes" but does not rotate, then either the starting capacitor is faulty (see Section 53) or the pump is jammed.
In those cases where the drive motor allows the speed to be changed and the regulator is set to the minimum speed, check if the engine has enough power: the motor torque must always be greater than the pump resistance moment (see section 55).
B) The starter is closed, but the pump does not rotate
First check the motor supply voltage. Make sure that the fuses or the cut-out (item 1 in figure 92.3) are closed, then check the voltage at the terminals (key 7). If there is no voltage, check the power circuit, just as we described above.
If the voltage at the terminals (key 7) is, measure the current in each phase with a clamp meter! Measuring the current absorbed by the motor is the most reliable way of controlling the operation of the pump if it is rotating (see Section 93.2).
Indeed, the pump impeller may well remain stationary (gauges installed at the pump outlet will not change their readings after the engine starts), while the motor will draw current from the network (for example because the impeller scrolls on the axis). Note that in this case, the current consumption of the motor will be very low, and the pump will emit a characteristic "bounce" (as if pans in the kitchen clatter).
Check the connecting wires between the starter terminal box and the motor winding (motor terminal box) and the voltage on the motor terminal box (item 8 in Figure 92.3).
If the three-phase AC motor is designed to operate at two mains voltage values, check the motor winding connection diagram (see section 62.1). In any case, do not be too lazy, remove the terminal box cover and look at it from the inside: as a rule, on the inside of the cover the connection diagram of the windings is given.
Note. Some small single-phase motors are equipped with a built-in thermal protection ("klixon" - "clicheson" relay), which disconnects the motor from the network when the temperature of the winding rises to the maximum permissible value.
At this time, the current consumed by the motor is zero, although the supply voltage at its terminals is present, and the motor housing is hot by touch. Remove the power from the motor (the coil will soon cool down) and check the ease of rotation of the shaft (see Figure 92.4).
D) Mechanical malfunctions
Depending on the design of the pump (see section 90), a wide variety of mechanical faults can prevent the free (easy) rotation of the shaft.
Dirty water with aggressive impurities or scale causes the scum, dirt or other impurities to clog the space between the rotor and the stator in the pump with the "flooded" motor rotor and the pump rotor "wedges". In addition, this dirt can cause seizure of bearings or sealing glands. The impeller can be jammed with a foreign body (a rag, forgotten in the pipeline during installation, deposits of scale or dirt, etc.).
Therefore, first of all, you should make sure that the axis of the motor is freely rotated by hand without any effort.
On pumping units with a coupling (item 1 in Figure 92.4), it is very easy to make sure that the shaft rotates freely. Turn off the motor power, grasp the sleeve sleeve by hand and try manually turning the shaft. In this case, you will also be able to verify that there is no excessive play of the clutch, evaluate the degree of wear and check the stiffness of the clutch. Also check the oil level (item A). If there is a need for oil refilling, use only the brand recommended by the pump manufacturer.
For a pump with a "dry" rotor (item 2 in Figure 92.4), remove the supply voltage from the motor and use a screwdriver or other suitable tool to turn the motor axis (coin, hexagon, etc.) and check the ease of rotation .
Some models with a "submerged" rotor of the engine (item 3 in Figure 92.4) are equipped with a screwed stopper with a plate shank (which sometimes serves as a drain cock) mounted on the shaft end.
On other models, you need to remove the sight glass to get to the shank. As a rule, when removing the sight glass, the pump does not lose its tightness.
The jamming occurs mainly after a long pump stop. The most common way to eliminate jamming is using one of the methods described above. Otherwise, you have to close the shut-off valves (if only they were sealed), and then disassemble the pumping unit to get to the impeller and turn it along with the axis.
Further, after starting the pump, it will be necessary to make sure that the current consumed by the engine does not exceed the value indicated on the nameplate of the engine.
In the example in Fig. 92.5, the motor is supplied with a voltage of 380 V, at which the nominal value of the current consumed by the motor must in no case be higher than the specified value. In addition, the fuse must also be set to a maximum current value of 1 A (see Section 55).
In pumping units with a coupling (see Figure 92.6), the excess of the nominal current consumption may be due to excessive tightening of the gland seal (see Section 90).
After replacing the sealing cord or during the gradual tightening of the stuffing box, always check the amount of current absorbed, not exceeding the value indicated on the nameplate of the engine.
During normal pump operation, the current consumed by the motor is mainly dependent on the amount of water flow through the circuit. The rated current indicated on the nameplate of the engine is extremely rare, except when the temperature and water pressure in the circuit approach extreme.
Never adjust fuses by the amount of current,
which is the value indicated on the motor nameplate.
This rule is valid for all electricity consumers (pumps, fans, compressors, etc.).
Repair of drainage pumps is a very important solution to the problem for long-term operation of devices in good condition. It's no secret that this unit will not be replaced for its sites during the thawing of snow or torrential rains, when excess water can do a lot of damage to the structures, flooding the cellars or washing away the foundation of the house.
With the help of a drain pump, water can be pumped from the pool or pit, or from any tank. How to repair a drainage pump with your own hands offers to get acquainted with this article.
What are the types of drainage pumps
According to their purpose, such pumps for pumping out dirty liquid are divided into:
- . This type of device is used for pumping liquids from small tanks.
The unit is installed on the ground, at the edge waste pit. To drain the waste, a hose is lowered to the bottom of the container.
When the pump is running in automatic mode, it is necessary to bring it to the switching lever float mechanism, he will monitor what level of water in the reservoir or foundation pit. When the sewage is raised above a certain mark, the float with them rises and turns on the equipment.
Such a device must have two pipes:
- entrance, to draw water from the sink pit;
- the output through which the liquid is withdrawn beyond its limits.
When working, make sure that no water gets into the engine, which can lead to damage to the machine. Therefore, the transfer of effluents must be carried out faster than their level can rise in the excavation.
Tip: Pumps are piped to the sewer system through the pipes. In this case, when mounting the unit, it is necessary that the diameter sewage pipe was known fairly accurately, up to a millimeter.
The main advantage of surface drainage devices - their mobility. The device can easily be moved to any place, and need to repair it can be done easily and quickly.
- . Such models are most often used for cleaning deep vessels and for large-scale floods, for eliminating excess water. In this case, the aggregates are lowered into the tank or trench, where it is necessary to pump out the liquid, and the water is sucked through the holes located in their bottom, and not through the inlet hoses for drainage pumps.
The mesh filters of the apparatus protect it from the ingress of stones and other large particles into the pump impeller.
The use of a float or a plastic bubble allows, with a certain volume of drains, to automatically switch on a submersible pump. To prevent possible shortages, when the device is immersed in a liquid, manufacturers have provided a quality electrical insulation.
The indisputable advantages of drainage pumping equipment for liquid are:
- Versatility.
- Long service life.
- There is no need for mandatory regular maintenance.
If it is necessary to pump out or pump a heavily polluted liquid, it is better to prefer sewage or faecal pumps. They have a special cutting or chopping tool and can pump and process liquid in which there are large household waste.
Tip: In this case, it is better to use an automatic sewerage system that allows the commissioning of bathrooms that do not have a connection to public sewage.
Device and principle of operation of drainage pumps
The main elements of the drain pump are:
- Engine. If the price of the pump is a small engine is located in the inner housing, made of plastic.
- The condenser motor, which has a thermal protection switch that prevents overload, has more expensive upgraded units. Here:
- the cases are made of high-strength polypropylene, reinforced with fiberglass; it is possible to manufacture the pump body from stainless steel or plastic, and for the motor housing and shaft is taken stainless steel;
- the working shaft is made of stainless steel.
- The case is internal.
- The case is external.
- or impeller, are located on the shaft in the outer casing of the pump. The configuration of the wheel determines how much dirt particles can pass the pumps.
When the pump is running, the space between the housings is filled with water, forming a "jacket" for cooling, which protects the unit from overheating.
- For automatic shutdown and start-up, the pumps are equipped with float switches that control the water level in the tank, protect the device from "dry running" and from flooding, monitor the timely activation of the pump.
Quality, and with a long pump life, work can be obtained if the content of fibrous inclusions is minimal, and the size of solid particles does not exceed 5 mm. The smaller the installation depth, the better.
Advice: The operation of drainage pumps with increased sewage temperature is limited by the time specified in the operating instructions. This is due to the fact that the cooling of the engine occurs when heat is released into the liquid that is pumped.
What are the criteria for selecting drainage pumps
There are several rules that must be observed when choosing an assembly:
- Take into account the type of pumped liquid. Determine how much particle it can pump without problems.
- To study the main parameters of the drain pump, which will help to choose the most suitable model. These values include:
- head. This value for an average product is approximately from about 7 to 10 meters. At high-pressure models it is possible to achieve a pressure more than 30 meters. Indicators of the head of the device will depend on the distance to which the liquid will be fed;
- performance. For example, for a 40 m3 tank, a device with a capacity of up to 10 m3 / h is sufficient. To use the units for industrial purposes, models with a capacity of 100 m3 / h and even more are required;
- depth of submergence of the pump. Its maximum value can vary from 5 to 15 meters, and the minimum is only from 0.3 to 0.9 meters.
Tip: It is mandatory for the unit to operate, its pumping part should be located under water.
The general view of the drain pump is shown in the photo.
The life of the device has a direct effect on:
- The quality of the material used to manufacture the elements of the device.
- Temperature of pumped liquid. It should not exceed + 50 ° С.
- The diameter of the conditional pass. This index affects the amount of suspensions and solids in the liquid.
- Presence of protection against overheating. Most often in the models are built in just two devices:
- float switch, needed to prevent engine overheating;
- thermostat, turns off the power when the water level has reached a critical level.
Repair of submersible pumps
Sometimes there is a situation when you need a repair. In this case, it is necessary first to find out the cause of the failure.
Most often this can be:
- Improper operation of the equipment - exceeding the operating parameters of the device.
- Long period between maintenance.
- Work unit in a "dry". If the pump is used for a long time in this mode, the pump may fail.
- The solid inclusions in the pumping liquid are too large.
- The installation of equipment has not been carried out qualitatively.
- Defective: relay, accumulator, no filter, there are other manufacturing defects.
All of these causes can lead to rapid wear and damage to the device.
If the cost of the unit is too high, it can be repaired drainage pump with their own hands, but only for those who have the skills to handle such aggregates.
When the first signs of malfunctioning appear submersible pump It is required to check the status and working capacity of such elements:
- The piston must have elasticity, on its form there should be no deformations or any mechanical damages.
- When blowing air on the side of the intake of liquid, it must pass freely on both sides.
- Between the piston and the coils of the electromagnet, the optimal distance should be from 0.4 to 0.5 cm. For larger intervals the coils will be beaten, with less - the motor will overheat.
- Between the valve that covers the inlet openings and the housing, the clearance should be between 0.7 and 0.8 mm.
Tip: Very often the poor performance of the equipment is caused by the failure of any elements, and the voltage drop in the mains. Therefore, before starting disassembly and starting self-repair of submersible pumps, it is necessary to initially check the voltage in the network, it should be 200-240V. If everything is normal here, you can start disassembling by making a special notch on the areas to be joined at the junction.
How to self-repair a drainage pump in detail shows the video in this article. Only the timely elimination of malfunctions in the operation of the unit will allow to operate it for a long time without any problems.
The drain pump is an integral device in the everyday life of any inhabitant a country house or cottages, because with his help you can provide a full water supply site (watering the garden and garden, water supply of the house, etc.) or drainage of waste water. Submersible or surface devices are considered durable and reliable instruments, but, like any other technique, they are not permanent. Therefore, in this article we will consider all possible malfunctions and self-repair of the drain pump.
Common Faults
Buying even the most expensive station can not be sure that once it does not happen a breakdown, and most often the equipment can fail for the following reasons:
- initially wrong installation of the device;
- absence of contact of the pump with water, that is, work "on dry";
- unstable food, namely - frequent drops and drawdowns of the network;
- contaminated water with a high content of abrasive particles;
- the power cord is damaged or improperly installed.
Often, equipment breakdowns are very commonplace, and due to their high cost, repairing the drainage pump with their own hands can be a good alternative to saving the family budget.
The most common failure of pumps is the failure of the pressure switch or accumulator, due to the absence of a filter. There are also cases of defrosting or the absence of a grounded loop on the device casing.
At all. all possible failures are divided into electrical and mechanical. For example, strange foreign sounds at start-up or during operation of the device testify to mechanical breakdowns. Such damage to the device can be completely corrected independently, but electrical defects can lead to a complete stop of the device and subsequent repair only in a specialized service center. Although the breakdowns on the electrical side are very common, for example, a safety switch has tripped, or the supply cable has disappeared.
Preliminary inspection of the drain pump
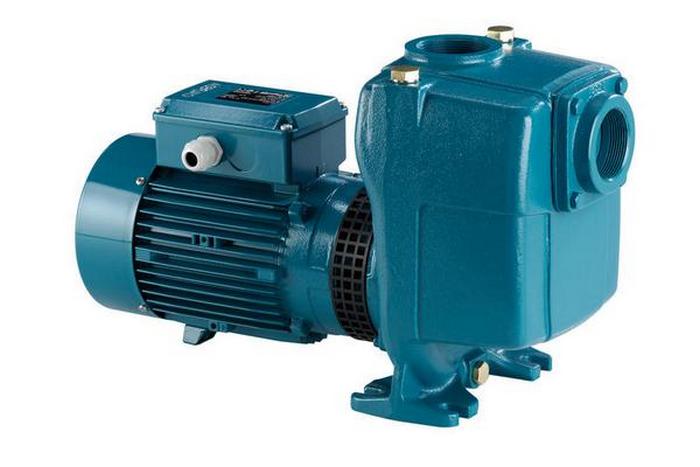
Before you begin repairing the drain pump yourself, you'll have to inspect it or even disassemble it. If the visual inspection has not yielded any results and everything is in order with the device, and you checked the voltage in the network and it corresponds to 200-240 V, you should disassemble and check the main components for the following faults:
- No deformation and damage to the piston;
- Make sure that there are gaps between the magnetic coils and the piston, which should correspond to 4-5 millimeters. A smaller distance will lead to overheating of the devices, but more will entail a battle of coils;
- Presence and free passage of air from the intake side of the pump;
- Inlet openings must have a gap between the body, namely at the place of installation of the valve. For a full-fledged supply of water, a gap of 7-8 mm is needed.
Popular pumps and problems with them
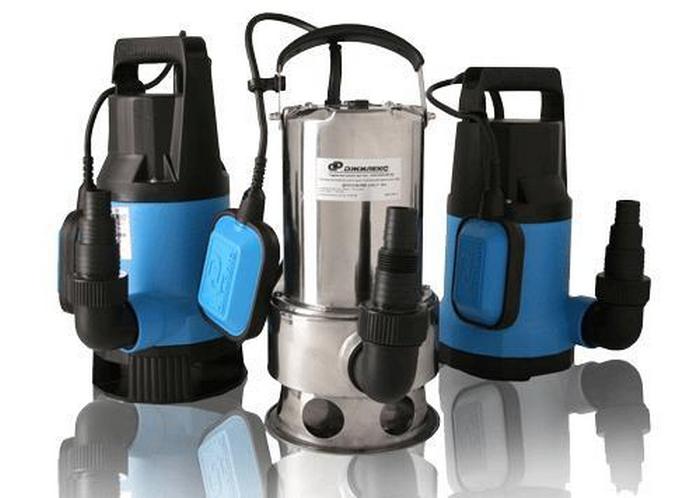
When choosing a drainage pump, it should be remembered that there is nothing eternal and even a high-quality apparatus can one day break down. Having considered numerous reviews and interviewed a lot of experts in the repair of equipment, several distinguishing features of each device were highlighted:
- Domestic drainage pump "Malysh" is very popular. The reason for such fame is the low cost of the product itself and the acceptable price for spare parts for repairs. Also, craftsmen easily repair their own. The most common malfunction of pumps "Kid" is the rupture of the swinging diaphragm. Symptoms of a malfunction are strong hum and lack of water pressure. Repair is performed only by replacing the torn membrane with a new one.
- For pumps "Dzhielek" such problem as loss of engine oil is inherent. The repair is carried out in the service center at a similar factory. There is an opinion of home-owners that the liquid from the engine can be replaced with glycerine or transformer oil. But this information is not verified, and such an alternative can lead to a complete breakdown of the pump.
- Drainage pump "Water meter" is famous for its reliability and most often the breakdown of this equipment is associated with improper use. Like other apparatus, "Vodomet" does not tolerate abrasive particles, such as silt and sand. If this happens, then you have to change the whole pumping part.
- Grundfos drainage and faecal pumps are very reliable, with most models having improved motor thermal insulation and built-in valves. Since the devices operate in an aggressive environment, the pump should be removed from time to time and all seals replaced.
- Surface and submersible models of pumps "Brook" produce according to the highest European quality standards, but they have one significant drawback - it is overheating. According to the statements of the manufacturers, their products are capable of continuously working for 7 or more hours, but as practice shows, this indicator is 2-3 hours after which the pump should "rest".
- As in the drainage, and in the fecal pump "Aquarius" there are problems with overheating of the motor, especially when used in small wells or wells. If an inexpensive model of a pump breaks, it is easier to replace it with a new product, since repairs cost half the cost of equipment.
Operation of automatic devices at pump start-up
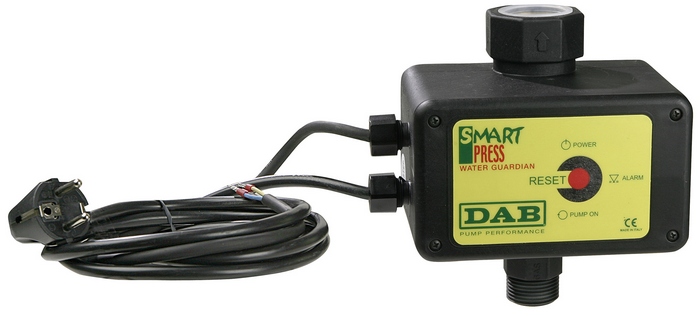
Knockout of plugs when the pump is switched on indicates a short circuit in the circuit. Consequently, the closure occurred in the power cable or in the worst cases in the anchor of the device. To determine where the drain pump broke, you'll have to get a tester or a multimeter. When the device is cured from the well, washed and dried, a visual inspection of the cable is performed, and in case of not detecting the problem, a test by the tester.
Advice! When repairing surface devices completely to disconnect it is not necessary, the main thing, turn off the power and make sure there is no pressure in the water supply. It is important to know! Replace the wire sometimes can be problematic, because in some submersible and surface models of pumps have the cables embedded in the casing.
If the cable is full, then only the version with the burnt anchor remains, but in this case it will be extremely problematic to do without the services of the service center. As an option, he will ask for help from a good electrician who can rewind the armature winding.
Noise, but not shaking
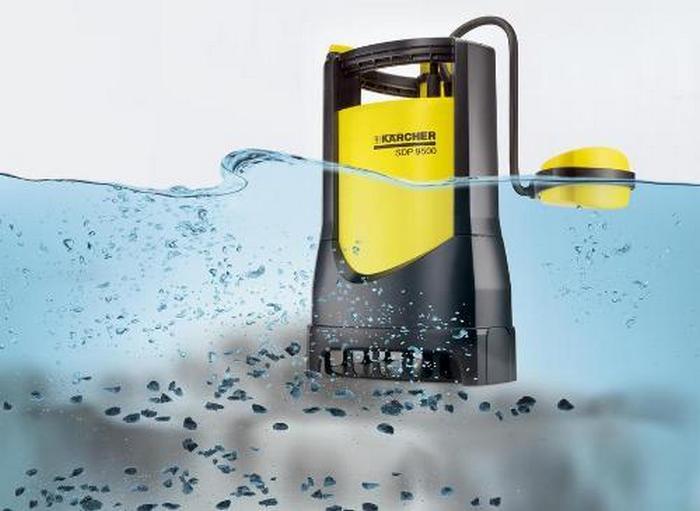
Another common problem that a drain pump may have is noise during operation and weak or no water pressure at all. The cause of pump breakage may be an unscrewed shock absorber, or, rather, weakened two fastening nuts. Also, the faulty valve may become the worn out valve or its full rupture.
To solve the problem with the membrane, Naos will have to be disassembled to reach two nuts located behind the membrane and tighten them to the stop. If the device has been in the water for a long time, the screws that tighten the body can be rusted with a WD-40 liquid and try to unscrew it after a while. If after these manipulations the bolts still do not open, they will have to be cut off by the Bulgarian.
The problem with the valve can only be solved with a complete disassembly of the device and subject to the availability of repair kits. Otherwise, you can not do without the services of a service center.
Vibration and overheating of the pump
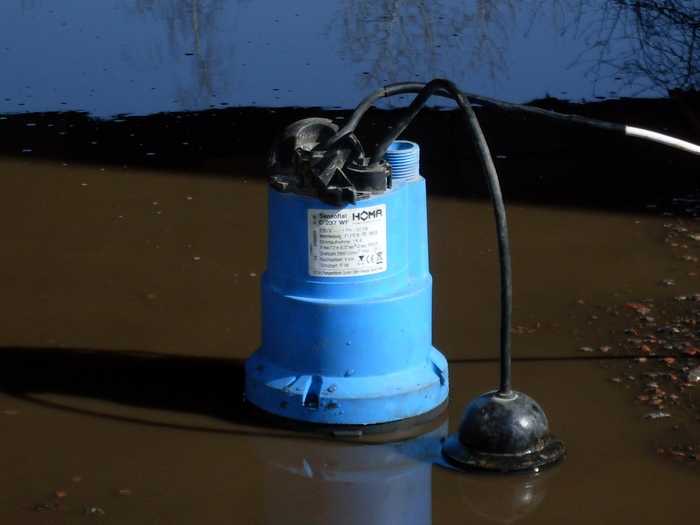
If the drain pump is not equipped with a special thermostat, which in case of overheating disconnects the device, it will have to be carefully monitored so that the device does not work "dry" for a long time. Since the cooler of the pumps is the liquid that it pumps and, having worked for a long time without water, the pump casing can overheat. Due to overheating, a magnet fixed in the casing with a special epoxy adhesive can move and jam the transfer piston.
After detaching the magnet in the pump, a chain reaction occurs, which leads to breakdown of all electronics and mechanics, and, consequently, the pump becomes just a heap of debris. According to experts, such a breakdown is the most difficult in terms of repair and often is economically impractical, of course, if you catch yourself in time and find out a breakdown in time, you can get by with "little blood", and, after giving the device to a service center, the magnet will be replaced, and damaged parts will be replaced.
Of course, you can try to repair the drain pump yourself, but there is a big risk of doing something wrong. For self-repair, the device is completely disassembled and the magnet is carefully removed. Then, a shallow longitudinal incision is applied to the magnet and pump body using a grinder or other device. And the final stage is the application of a new epoxy glue or glass sealant, as well as reassembly and replacement of worn parts.
Weak output pressure
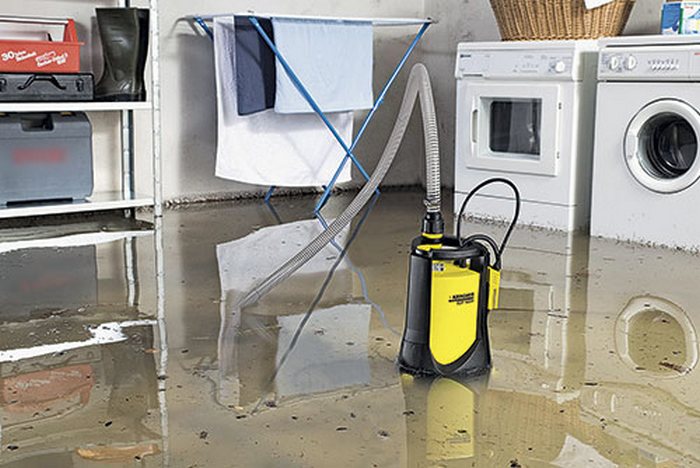
Submersible and surface pumps often have such a breakdown as weak output pressure. The reasons for such a breakdown may be several:
- Clogged filter. If the filter grid is clogged, the water pressure may drop or the supply may stop completely. Symptoms of clogging are the operation of the device in the load and increase in noise, and also the motor overheating may occur.
- Surface stations can have damaged pipe or weakened clamp, as a result of which air is sucked in and the pump is not able to lift water from the well. The solution of the problem is trivial - check the condition of suction pipes and clamps.
- If everything is in order at the pump inlet, then only variant with a small stroke of the vibrator. This problem is solved elementary, you need to disassemble the device and put a washer on the vibrator rod.
Advice! It is mandatory to check the condition of the membranes and seals, they must be intact and without damage.
Perhaps, it is necessary to put a few washers, all this is determined by experience.
Conclusion
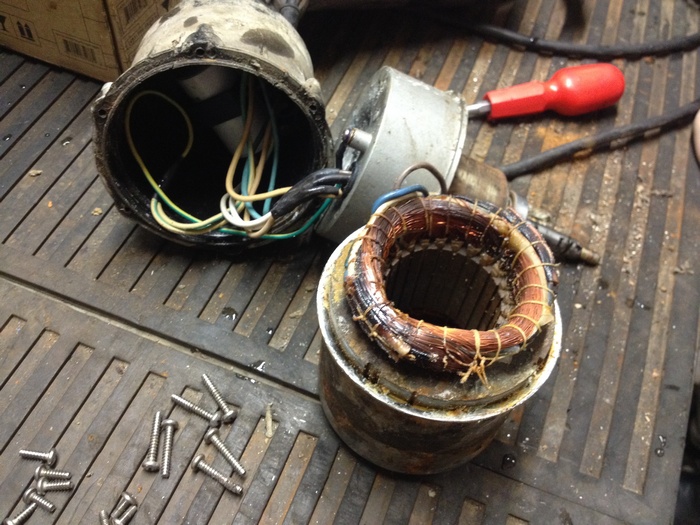
In the article, we listed the main malfunctions that have submerged and surface drainage stations and possible ways of their repair. For self-repair, you need to have at least initial skills in working with devices, otherwise it's better to contact the service center. After all, what is a drain pump for? Properly ensuring a comfortable life in a country house or the country house. But the repair and maintenance of such devices should be handled by specialists. If you like to pick your own hands in various devices, then inexpensive models will be for you the best option, but for repairing expensive devices it is better not to undertake.
1.
2.
3.
4.
A drainage pump for the owners of household plots is in demand and indispensable equipment when it comes time to melt snow or a period of heavy rains. The fact is that excess water can inflict irreparable damage on buildings, flooding basements and eroding the foundation of buildings. During operation, sometimes it is necessary to repair the drainage pump. The photo shows what this device looks like.
The drain pump allows to pump the liquid from the pool, pit, tank, well, tank. Is it possible to eliminate the malfunction of it with their own hands, often consumers are interested in this product.
Types of drainage pumps
Such units for pumping out dirty water and drains are superficial and submersible according to their purpose (read: "").Pumps drainage surface. They are used for pumping liquids from small containers in volume. The apparatus is placed on the ground near the edge of the drain tank (read also: ""). To drain the dirty water, the hose is lowered to the bottom of the container. If the pump functions in automatic mode, the float mechanism must be brought to the switching lever, which will allow monitoring the level of liquid in the pit or reservoir. When the drains rise above a certain level, a float floats up with them and the unit turns on (in more detail: "").
The drain pump has two pipes:
- input - for the collection of dirty water from the waste tank;
- output - necessary for draining the liquid out of the container.
Advantage surface pumps is in mobility - they can be easily and quickly moved to another location.
Drainage Submersible Pumps. This type of apparatus is used, if necessary, to clean deep reservoirs, and in the case of large-scale floods, for evacuation of surplus water. The unit is lowered into a well or a container, where it is required to pump out the liquid (more: ""). Suction is made through holes in the bottom of the device, and not through the inlet hoses. To prevent large impulses from entering the impeller, there are screen filters in the pump.
The use of float switches allows a large number of drains to automatically turn on the device. Avoid the possibility of closure when you immerse the device in a liquid can be due to the presence of high-quality electrical insulation.
If it is necessary to pump out or pump liquid with large fractions, experts recommend using fecal (sewage) pumps having special cutting and cutting elements. They are able to pump and process effluents containing large amounts of waste. The most optimal solution will be the purchase of an automatic sewerage system, which will allow to operate bathrooms that do not have connection to centralized sewage systems.
The device of the drainage pump
Elements of drainage pumping equipment are:- engine - when the device is small, it is in the inner plastic case;
- condenser motor with thermal overload protection switch (in more expensive upgraded models);
- the body is internal and external - in modern, expensive units they are made of high-strength polypropylene reinforced with fiberglass. Also the cases are made of plastic or stainless steel. When the machine is operating, the space between the housings is filled with water, so that the unit does not overheat;
- working shaft is made of stainless steel;
- impeller or impeller are located in the outer casing on the shaft. The configuration of this part depends on the size of the particles of inclusions that the pump can process;
- float switch - serves to turn the machine off and on in automatic mode. This device controls the level of liquid in the well or the tank, providing protection of the mechanism from "dry running". It is responsible for the timely activation of the device.
The functioning of drainage pumps when transferring wastewater having an elevated temperature is limited to a time period - information on this is contained in the operating instructions of the manufacturer. The fact is that the cooling of the engine of the unit is due to the return of heat to the pumped liquid.
Criteria for selecting drainage pumps
There are several rules that should be followed in the case of the choice of apparatus:It is necessary to take into account the type of pumped liquid - here pay attention to the size of fractions in dirty water. It is necessary to familiarize yourself with the main parameters of the drainage unit in order to stop your choice on a certain model.
First of all:
- pressure - this value for medium-capacity equipment is 7-10 meters. In some models it reaches more than 30 meters. The data on the pump head depends on the distance to which the liquid is to be dispensed;
- performance - the choice depends on the volume of the tank. For example, for a capacity of 40 "cubes" there is enough apparatus with 10 cubic meters per hour. For industrial purposes, more productive pumps are needed - about 100 m³ / h and more;
- depth of immersion apparatus - the maximum given value reaches 5 -15 meters, and the minimum - 0,3 - 0,9 meters.
In addition, you need to know, from what moments depends on the life of the pump:
- the quality of the materials from which the elements of the equipment are made;
- temperature of pumped dirty water, it should not be more than + 50 ° C;
- diameter of the drainage passage;
- presence of protection against possible overheating. Usually a thermal relay is built into the pump (it will turn off the power if the temperature of the liquid becomes critical) and a float switch.
Repair of drainage pumps
When the drainage pump breaks down - malfunctions are eliminated after finding out the cause of the breakdown.Most often it happens:
- improper operation when the operating parameters of the apparatus are exceeded;
- a long period between maintenance;
- long-term operation of the device in "dry" mode;
- very large solid inclusions in the pumped liquid (then the drain pump does not pump water);
- poorly produced pump mounting;
- production defect.
When the device is inexpensive, the drain pump is dismantled and it is repaired by one's own hands, provided that you have the skills to handle such units.
If there are first signs of malfunctioning of the submersible pump, you need to check the operability and condition of the individual elements:
- the piston must be flexible and can not be mechanically damaged;
- it is necessary that air blown on the site of the intake of liquid freely pass on both sides;
- the optimal distance between the piston and the coils of the electromagnet is from 0.4 to 0.5 centimeters. If the gap is greater, the coils are beating, and when less - the motor overheats;
- between the valve closing the inlet openings and the housing, the gap should be between 0.7 and 0.8 millimeters.
Often, the cause of poor operation of the equipment is not the breakdown of individual elements, but the voltage drop in the electrical network. Before dismantling the drain pump and starting to repair it yourself, it is necessary to check the voltage in the network, which should be 200-240V. If this parameter is normal, you can start disassembling by applying special notches on the areas to be joined.
If the drain pump does not pump, which is in working order, the possible reasons are as follows:
- the air intake got into the water intake part;
- insufficient depth of immersion of the unit;
- the water intake element is not covered with liquid.
Only with the condition of timely elimination of malfunctions in the operation of the drain pump will it operate for a long time without serious problems.
Repair of the drainage pump by one's own hands, alas, is not always possible. Certain faults can only be eliminated by specialists in the conditions of a specialized workshop. Some failures can not be fixed at all - it will not save even the replacement of the part, you will have to buy new equipment. The list of self-fixes is short, but consideration is still worth it.
- the motor drives the impeller fixed to the shaft;
- the impeller plates disperse liquid inside the pump casing;
- under the action of a centrifugal force, the liquid enters the outlet;
- the vacated place immediately takes up the liquid that enters through the inlet.
The holes are located at different levels. It depends on the type of pump: submersible, surface. Submersible take water from below, and not from the side.
Diagram of drain pump
Video: Dilax Drainage Pumps
Unplanned repairs by one's own hands or in the workshop will not be necessary if you follow the simple rules of operation of equipment detailed in this video clip of the manufacturer. It also tells about the principle of the device.
Basic malfunctions of drainage pumps
The pump does not work if:
- There was a short circuit due to a sudden voltage drop in the electrical system, the winding burned.
- The float (if it's a float device) jammed below the trigger level (keep the well walls, hoses, power cable).
- The impeller jammed with mechanical inclusions trapped in the body.
- The capacitor has failed.
The pump does not work, but it hums if:
- The valve has failed.
- The mounting of the shock absorber on the rod is loose.
- Stock stopped.
- The power cable is out of order (the wires inside the common cable have been frayed).
The main malfunctions are listed. Diagnosis is required to identify individual breakdowns.
Important! Before you beat the alarm, first check the network - maybe problems with electricity, and not with the pump.
How to repair a drain pump yourself
Of all the listed faults of drainage pumps with their own hands, only a few can be eliminated. Really release the float (here instructions are hardly needed), remove the wedged impeller mechanical inclusions (you can not tighten the impeller, as in the video below), fix the shock absorber, repair the cable. To secure the shock absorber, it is necessary to disassemble the body and simply tighten the nuts on the mounting bolts by screwing the upper one. This is the simplest of all. Cable repair will take time, but it's feasible. In some models it is easy to replace the capacitor.
All the rest is not done without the masters, and the ragged stock in general is so difficult to fix, that the acquisition of new equipment is much more expedient. It will not be possible to replace the valve yourself (difficult, unprofitable) and repair the winding - a specialized tool will be required. However, this does not apply to cheap Chinese pumps: they either take new ones or repair themselves, since highly qualified repairs will cost more.
Video: repairing the drain pump yourself
The citizen tells us how to fix the device, and what mistakes he made while doing this - the anchor was damaged, the impeller broke (oh, and the Chinese impellers are strong). A person works cheerfully, on a pair with a TV, that's why it's very difficult to hear a lot, but everything is perfectly visible. With his own hands, he only broke in the beginning, and then he repaired.
Repairing the drain pump power cord
If the power cord fails, the pump will not turn on (obviously), but sometimes the fault can not be detected visually, that is, the wires are torn inside the insulating cable.
Before trying to repair the cable, you need to understand where it is broken. The two most probable are the place of connection to the pump, the length at the fork - that is, the most frequently bent areas. Here you need a medical method - palpation. That is, you have to squeeze your fingers with your fingers so that the torn wires are connected (they can not get out of the submarine anyway) - thus you will find the breakage place (if you do not forget to turn on the equipment).
To fix the cable broken at the entrance to the housing, it must first be removed. Demolition is required. Here surprises may await: in some GNOM-x bolts are not designed to be twisted with normal screwdrivers - they are made for a 3-petal bit (rare, now hexagonal holes are more often). The manufacturer's motivation is unknown.
Important! When removing the cover, do not pull it, do not tear it sharply - you can accidentally break off the wires, and they will entrain the winding of the motor. Gently swing, gradually the lid will loosen.
Inside the case there is a tensioning device. It must be removed by unscrewing the 3 bolts. Remove the tension washer. Remove the cable. Cut it further off the wire break and insert it back. Here, another surprise may lie in wait - the swollen cable will not pass into the hole intended for it. It will be necessary to lubricate it with engine oil (it is better not to consider the option with removing the coupling: you can disfigure the part).
All detachable wires need to be labeled, so that they can be properly connected without interrupting the "ground", "zero" and phase (ground wire, usually yellow-green, "zero" - blue, but anything can happen).
After inserting the cable, replace the tensioner, tighten the bolts, assemble the circuit, isolate the connections. When installing the cover, make sure that the stud is in the groove. Do not press.
We talked about idle pumps. It also happens that the pump turns on, but then turns off - it is able to work, but for some reason does not want it. Such a behavior of the device is explained either by a short circuit in the circuit or by a blockage in the flow region. It is not difficult to check the circuit and repair the malfunction (the closure in the pumping equipment circuit is no different from any other closure). If in the process of checking the circuit, it was not possible to detect the fault, the matter is in a clog. Remove the filter, the diaphragm, and clean the flow area.
If the pump stopped pumping as much fun as before, the worn impeller most likely worn out - it is necessary to change. The widened gap between the impeller and the diaphragm can also cause a decline in equipment performance. The gap must be adjusted.
In order to prevent and prevent blockages in the flow area, it is recommended that after running the pump with contaminated fluids run it in clean water - this will help to remove as yet not accumulated impurities.
Important! Be sure to disconnect the equipment from the network, if you are going to look for breakdowns - do not forget about safety.
Independently little that can be repaired (even the bolts adjust the trick, even the replacement of the wire is surrounded by difficulties), and therefore we must protect the equipment. Here, as with crimes: the best method of struggle is prevention.
If the drain pump has to work in inappropriate conditions, it will fail. The drain pump does not cope with large inclusions (the permissible fractions are specified in the instructions). If such inclusions are suspected, use a fecal pump with a chopper.