How to solder heating yourself. Reinforced polypropylene pipe - how to solder? Which tool
Polymer pipes for the construction of heating water are used for more than a dozen years. They have a lot of advantages, including the simplicity of connection technologies, which are durable and durable. The high quality of the connection of polymer pipes, namely the tightness of the joints, is due to the features of the polymer material and the mounting technology based on these features. The process of connecting the fragments of the heating pipeline, which in everyday life is called soldering or welding, is technically available for independent execution and does not require an expensive tool. Therefore, the installation of plastic pipelines often produce on their own, acquiring the skills of soldering during the execution of work.
To make these skills easier and with less errors, let's consider the process of soldering polymer products in more detail.
The following types of plastic pipes are made of plastic:
- polyethylene (PE);
- of cross-linked polyethylene (PE-X);
- polypropylene (PP);
- polybutene (PB);
- from polyvinyl chloride (abbreviation Cyrillic - PVC);
- fiberglass plastic;
- from metal plastic.
Of the listed materials for the installation of the heating system are suitable polypropylene, cross-linked polyethylene, high-temperature polyethylene, polybutene and metal-plastic. And of these five heat-resistant materials, only three can be joined by soldering.
Soldering pipes for heating:
- polypropylene (PB);
- from polyethylene of the raised heat resistance (PE-RT);
- polybutene (PB).
The technology of welding these types of pipe products has both common for all materials components, and individual, inherent in only one variety, features.
The essence of the process and methods of soldering polymer pipes
Welding of polymer pipes is used to connect the fragments of the pipeline to each other, the sidebar into the heating circuit of the stop valves, measuring, monitoring and safety equipment. The connection of the joints of these components of the heating system is carried out in three ways, each of which is essentially a technology closer to soldering or welding, but for simplicity can be called both terms:
- diffusion - the method of joining by applying a compression force at an elevated temperature without the use of solder (welding);
- electrofitting - diffusion differs only in the design of fittings and in the automation of the process (welding);
- cold - joint fragments using an intermediate, solder (soldering).
The first two methods are the penetration of the molecules of the connected surfaces into each other under a compressive load after heating them to a certain temperature, which is typical for welding.
The cold method consists in the mechanical preparation, cleaning of the surfaces to be joined, applying welding mass to them and connecting the products with short-term fixation in the working position necessary for setting the solder, an element of the soldering process.
The latter method of connection is less reliable, but it is convenient for mounting fragments in hard-to-reach places.
Tool for connecting heating pipes from polymers
For each method of installation of plastic pipe products, there is a certain set of tools, basic and auxiliary. Without some of them, auxiliary, you can do without, replacing them with similar ones.
Tool for diffusion method of installation of polymer pipes
To perform the diffusion connection of tubular products from plastic, a set of tools is also required, each of which is intended for a certain operation. Consider these adaptations, placing in the list in the direction of decreasing the degree of significance.
Welding machine for connecting plastic pipes
This is the name of a special electric welding device, commonly known as a pipe soldering iron or iron.
According to the shape of the hull and platform, soldering tools are divided into xiphoid and cylindrical designs, and it's not just a matter of visual difference.
Apparatuses xiphonous execution in household applications are more common, since the device attachments on these models is simple, and the price of the tool in this regard is lower.
Soldering irons with a cylindrical body are more compact, the configuration of their nozzles is more complicated, and the fixation is stiffer. In addition, the operating temperature of cylindrical irons is more stable - its differences between cyclic inclusions and offs are less in value. Therefore, the cost of such an instrument is higher, and it is used mainly by professionals.
The device of a pipe soldering iron
The apparatus for brazing polymer pipes consists of the following elements:
- housing with handle;
- cast platform of triangular (xiphoid) or cylindrical shape with the possibility of attachment of nozzles;
- thermoelectric heater (TEN) inside the cast platform;
- thermoregulator;
- teflon-coated removable nozzles for various pipe diameters;
- indicator lamps for heating and tool readiness for operation;
- a tripod for mounting on a horizontal surface;
- power cord.
Characteristics of the apparatus for welding plastic pipes
The main parameter of a pipe soldering iron is power, since it determines:
- the largest diameter of the polymer pipes welded by this apparatus;
- heating speed of iron;
- productivity - as a consequence of previous factors.
However, when buying a device for domestic needs should not be guided by the principle of "more powerful - better." In this case, the unclaimed surplus of power is an unnecessary expense in the form of a higher cost of the device and not a rational consumption of electricity. The optimum power of a soldering iron for domestic needs is determined by a simple calculation: the maximum diameter of the pipes used in mm is multiplied by 10 and the minimum value in watts is obtained, to which it is necessary to add 10%. For example, for welding polypropylene pipes with a diameter of 40 mm, an iron of minimum power of 400 W is needed. If we take into account that in a private house plastic pipes with a diameter of more than 60 mm are not used in the heating device, then the maximum power of the apparatus will be 700 W for welding.
If you take into account the likelihood of doing third-party orders, then you need to purchase a more powerful iron (1.5 - 1.8 kW), through which you can perform the connection of pipes with a diameter of 100 mm or more.
Approximate values of the power of the tool with reference to the diameter of the pipes:
Thus, the power of the welding machine and the diameters of the nozzles to it are interrelated factors.
Important! By purchasing additional nozzles of larger diameter for the iron in the set, it is necessary to do this with reference to the power of the tool.
In addition to the diameter, the nozzles are also characterized by their performance - the value of the thermal conductivity (higher - better), as well as the thickness and quality of the Teflon coating. It is impossible to visualize this, but the experience of using irons by other masters will help - well-established models among professionals are fairly well-known, when buying it is necessary only to check the absence of mechanical damage to Teflon. As for the unofficial rating of countries producing pipe soldering irons, it looks like this:
- Germany;
- Czech Republic;
- Russia;
- Turkey;
- China.
For professional use it is better to purchase the tool of the first two positions, productive and durable. For occasional use, Chinese and Turkish products are suitable. Russian products are on the border between domestic demand and professional application, and with the right choice of capacity will also last for many years.
Scissors for cutting polymer pipes
This tool is referred to simply as a pipe shear, pipe cutter or pipe cutter. Pipe cutter provides fast cutting of polymer products without applying significant forces, performing the cutting edge without burrs, which simplifies the preparation of the pipe for welding.
There are 4 varieties of this tool, listed below in order of increasing complexity of design and cost:
- precision scissors with ratchet mechanism - simple and easy-to-use tool, differing in the maximum diameter of the cut pipes (up to 42 and up to 75 mm in diameter);
- automatic tube cutter in the form of a pistol - similar to the previous tool, but requiring less effort, universal for pipe diameters and convenient for cutting and dismantling a pipe fixed to the wall with one hand;
- roller pipe cutter - very convenient in use, the device that cuts the pipe by rolling it along the disk blade;
- pipe cutter-guillotine - a tool with a manual or electric drive, performing cutting of the fixed in the pipe clamp.
Tool for cleaning plastic pipes
If a polymeric pipe reinforced with aluminum foil is to be welded, the reinforcing layer must be removed, otherwise the monolithicity of the welding joint will not be achieved and the tightness of the joint will be close to zero.
The tool for this preparatory procedure is called a shaver, a cleavage clutch or the name of the operation - a sweep, and it is produced for two types of reinforcement.
If the foil reinforcement is located close to the surface, a different model shaker is placed on the tube cut, which, when rotated by its internal blade, removes the top layer of the product together with the aluminum and cuts the cut.
If the reinforcement is made in the thickness of the wall, the foil is removed to a certain depth from the groove between the polymer layers. Such processing of the joint before welding is carried out by a different kind of cleaning clutch.
Of the remaining tools needed for welding polymeric products, you can mention a measuring tape measure and a marker for drawing dimensional marks.
Tool for electrofitting installation of plastic pipes
The main tool and at the same time the installation part in this case is electrofitting - one of the connecting elements (coupling, branch, tee), inside of which there is an electrical heating element with outwardly exposed contacts. Therefore, the description of the instrument is also a brief instruction for the use of this equipment.
Connectable fragments are inserted into the electrofitting and fixed in a special device, after which the contacts of the fitting are fed via a time relay by a voltage from a special welding machine. Heating the element inside the electrofitting causes the polymer to melt the contact surfaces and firmly connect them through the fitting.
Advantage of the method is the simplicity of the technology and high performance of installation, which is important when performing large volumes of work.
The disadvantage is the high cost of the welding machine and the electrofitting of the connection, which causes unpopularity of this method of soldering at home.
Welding of cold plastic pipes
Cold brazing of heating pipes from polymers is carried out using a special welding mass (solder, glue). The composition of the solder includes components that soften the upper layer of the material of the contact surfaces of the parts to be glued.
The surfaces of the pipes are cleaned and degreased, and then the solder is prepared - depending on the consistency of the execution, mixed or softened, manually.
Then the welding mass is applied to the contact surfaces, and the products are connected. The connection is fixed in the working position for approximately half a minute (the fixing period is specified in the instructions for use), after which the joint is released, but the final strength will be collected after the day.
The joining of polymeric pipes by the method of cold welding by strength is not inferior to the diffusion method, but has a low thermal stability, so it is not used for heating - only for the installation of cold water supply systems, which is naturally a drawback.
Dignity is the simplicity of execution, which does not require the purchase of a special electric heating tool.
Implementation of polymer pipe connections
Let's consider the technology of performing the most common type of connection of plastic pipes - diffusion welding, for which we will list the sequence of soldering of heating pipes from polypropylene - due to the high characteristics of the polymer material that is in great demand today.
Roulette measure the desired length of the pipe, and in the place of cutting the marker is put at risk. Pipe scissors produce a control cutting of an unnecessary piece of material to check the sharpness of the tool and the quality of the edge of the cut. Then the required fragment is cut with a pipe cutter, and the end of the pipe is treated with a butt - burrs, foil are removed and an external chamfer is made.
Important! The cutting line of a pipe with a diameter of up to 50 mm is made perpendicular to the axis of the pipe. With a diameter of more than 50 mm, the butt is cut at an angle of 35-40% to prevent the pipe from collapsing when inserted into the fitting.
The required fitting is selected:
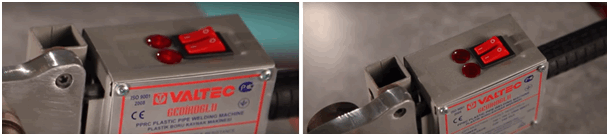
After an hour after the rations the pipeline is ready for operation.
The necessary data for the duration of thermal processes with reference to the diameter of the pipes are summarized in the table:
Important! Table data is calculated for an ambient temperature of +20 degrees. At its lower values, the heating time will increase accordingly, and one test connection will allow it to be corrected.
Conclusion
Welding polypropylene heating pipes - the operation is not difficult, but responsible. An error in performance or negligence is fraught with serious consequences even when the heating system is being tested, so it is better to perform it for the first time under the guidance of a mentor - the implementation process has many small nuances that in the absence of experience can be ignored.
The main essence of the article
- It is important to determine the list of materials for the manufacture of plastic pipes for heating, the connection of which is possible by soldering.
- Correctly to choose the tool - to save on manufacture of installation works.
- Compliance with welding technology - a pledge of high quality welding and reducing the probability of emergency situations.
Due to the special climatic conditions of our country it is very difficult to imagine an apartment or a house without a heating system. Surviving the winter without radiators or batteries is very difficult. Therefore, this article on the installation of a heating system made of polypropylene pipes, will be very relevant, especially in the run-up to the cold weather. Why, as the main material, we will use a polypropylene pipeline, you will learn from the next section of the article.
On the market of building materials you will find many different types of pipes, metal, plastic, etc. Polypropylene pipes are the most popular. Not only ordinary consumers, but their professionals, use their advice.
The prevalence of the heating system from polypropylene pipes is directly related to these positive characteristics:
- they are environmentally safe;
- are strong and reliable;
- have a long service life, polypropylene pipes can, if properly used, last for up to 50 years;
- pipes are resistant to external influences;
- not subject to corrosion;
- even after a long time, the pipes keep their inner surface smooth, which will allow the water to circulate quickly and unobstructed;
- simplicity in the montage;
- do not require complex machining;
- pipes of polypropylene have a low specific gravity;
- have a relatively low cost.
The only disadvantage of installing heating from polypropylene pipes is that the master must have a certain rigging when soldering with the help of a pusher. A less critical disadvantage is the low refractoriness of polypropylene.
If they decided to install heating with polypropylene pipes by their own hands , topokupat apparatus for welding is optional, it can take a varendou or ask for an ugliness.
How to connect polypropylene pipes? Basic methods
To create a heating system for polypropylene pipes, one has to understand how they can be combined. There are several types of soldering, they are divided according to the size of the tube.
If the pipeline has a diameter of up to 63 mm, then its parts are connected in two ways:
- fusion welding technology;
- by means of coupling welding.
The first method is the simplest. In simple terms, the principle of connection is as follows: one end of the tube enters the broadened end of the other.
The socket heating soldering by polypropylene pipes assumes the use of a special detail-coupler, which includes two connected parts. If a pipe connection is provided by the thread, it is necessary to use special socket fittings.
Pipes with a large diameter can be soldered "in butt". This is considered the most reliable method of attachment.
- hand-held welding machine;
- pipes made of polypropylene;
- heating element - sleeve;
- nozzles of different diameters;
- wooden spatula or rags.
A hand-held welding machine is suitable for connecting pipes with a diameter of up to 40 mm. For wider pipes, a fixed installation is required that will perform the preliminary alignment.
To transfer the heat initiating to the polymer elements, a heating sleeve is needed. It melts the outer and inner layer of the socket in order to obtain an expanded section of the tube. Due to the fact that the sleeves are covered with Teflon, the melted material does not adhere to the heating element. These parts are removable, so they can easily be removed after work.
Before starting work, the stationary device is installed so that it stays motionlessly inertized. Before connecting, all attachments are installed outside beforehand. To effectively connect the master to the welding, there should be enough free space, otherwise inaccuracies may arise. If you doubt your strength, it is better to apply for help to a professional.
Specialists advise to carefully monitor the surface, cleaning it of the remaining polypropylene. You can remove it with the help of a wooden spatula. Do this immediately, until the polymer has failed to harden.
Features of socket fusion
Installation of polypropylene pipes of the supplied technology requires certain requirements:
- cut the pipes at an angle of 90 degrees, preferably using a sharp knife or scissors;
- sarmirovannyh pipes need to remove the metal shell in advance;
- installation work involves the use of a welding machine, so proceed with the process of soldering only with gloves;
- further all the nozzles of the temperature of 260 degrees must be heated;
- to connect fittings it is necessary quickly and precisely, supervising process. The appearance of an uneven seam or misalignment is unacceptable.
- after soldering, the joint should be allowed to harden.
Requirements for heating installation with spilipropylene pipes
- At work, it is necessary to use materials without contamination of the needles, so when transporting the wound it is necessary to comply with all the requirements of the inorganic. Only clean and dried parts can create an airtight, ethereal connection.
- Polypropylene piping should be stored dry in a room, away from the open fire.
- When transporting, you need to be careful to protect the pipes from the mechanical effects.
- Qualitative soldering of pipes is possible in the room with a temperature of at least 5 degrees Celsius.
- When soldering pipes it is necessary to use connecting parts.
- You can not cut the threads yourself, when connecting pipes in this way you need to use special fittings.
- A reliable connection of the pipeline will be ensured if during the installation you will use a Teflon tape or other type of sealing fabric.
Installation and heating of polypropylene pipes: video
Designing of heating system
The most common is the heating of polypropylene pipes in the house . Usually independent installation work begins with the design of the heating system. The houses for the installation of the boiler provide for a separate room, in apartments it is often hung up with nakuchne or vpostrozhie.
Planning the heating system is a very important stage, the failure of its performance depends on the efficiency of heating the house or apartment in the future.
First of all, a heating scheme is made of polypropylene pipes. The figure indicates the number of radiators, the passage of walls and the number of turns of the pipeline. The heating system must be designed so that the return pipe is at the receiving end of the boiler. If it is below it, then the circulation of water will be difficult. Next, the design plan needs to calculate the length of the pipes and the number of fittings for the connection.
Installation of the heating system can be carried out by one of 2 schemes:
- overhead technology;
- after the bottom spill.
The first heating system is based on the heat-transfer agent due to the temperature difference. The upper spill is very common in the homes of Icottages, there is no need to especially spend the pump for its installation. In addition, this scheme is the most simple and reliable option especially for those who plan to mount the pipeline themselves.
The technology of the bottom spill is more complicated. It requires the running of water to the heating circuit forcibly. This is achieved by a special pump built into the heating system. Despite the additional costs, this scheme is popular in many-storey houses. Plus, the cow for its device can use pipes of smaller diameter.
In addition to the classification of heating systems described above, one-pipe and two-pipe schemes are singled out by lowering the bypass connection to the batteries or radiators.
Tips to help the heating system of polypropylene pipes
The device is fitted with a nozzle, it must correspond to the diameter of the tube. The end of the pipeline is combined with a snap and heated. The heating time depends on the size of the tube, for example, 20 millimeters of pipes warm for 5 seconds, pipes with a diameter of 63 mm should be kept 24 seconds.
After this procedure, their details should be tightly pressed to each other and held for a few seconds. The tight connection will be obtained after the parts have cooled down. Specialists advise to control the heating of parts, since overheating can provoke the appearance of adhesions inside the pipe.
After all installation works, it is recommended to check the quality of the connection. To do this, the wizard must organize the purge of the system. If there are no obstacles detected during the check, the work is carried out qualitatively, aswark-free of adhesions.
The article described the process of installing a heating system made of polypropylene pipes. Following the instructions, you can do all the work yourself without involving specialists.
Advantages of polypropylene (PP) pipes weight! This is the stability of corrosion, and durability, and lightness, and a smooth internal surface and much more.
Simplicity of installation is also an attractive factor. You can do everything quickly, without recruiting hired workers, with your own hands. How soldering of polypropylene pipes is carried out.
The instruction on three methods:
- Diffusion soldering.
- Electrofiting.
- Cold method.
Consider how to solder polypropylene by diffusion soldering. This is the most popular method among independent masters. The soldering iron is inexpensive (in some places it is possible to borrow a tool), and you can learn how to use it very quickly.
A pipeline layout is drawn up, a set of all its elements is selected: straight sections, corners, connecting parts, expansion joints. To the soldering iron the nozzles corresponding to the diameter of the pipeline are selected.
Then the device warms up to 260 ° C, the connection element is inserted into it and it is heated for several seconds (determined according to the table below), as well as the pipe from the outside.
During this time, the upper layer of plastic softens and when the elements are quickly inserted one into the other, adhesion occurs at the molecular level. The cooled pipe at the junction is already monolithic.
In general, this is the simplest and most inexpensive method. Disadvantages can occur only in hard-to-reach areas of the system.
The dimensions of the nozzles determine the outer diameter of the pipes and the internal diameter of the fittings.
Pipe connection using electrofitting
Installation will become even easier if you purchase couplings, in the construction of which are included heating elements, spirals. On the surface there are contacts, to which, at the moment of fixation, a welding machine is connected. It sends current to the contacts for a certain time. Instruction:
- Clean and degrease the surfaces.
- Insert the pipe into the fitting, fix it.
- By wires connect the electrofusion unit to the electrofitting contacts.
- Switch on the machine.
- Through the control holes on the fittings will be visible melting and increasing in volume plastic. The device will switch off automatically, and the smart machine adjusts the welding time, depending on the ambient temperature.
- Disconnect the soldering iron from the contacts.
Advantages of the method is that everything is done record fast and easy (soldering time - 1 second, cooling - 1 minute). Problems with hard-to-reach places will not arise, since the soldering process goes directly assembled on site, which is convenient when installing closed heating systems. In addition, it is possible to work by this method even in a small frost (down to -15 ° C, which is forbidden when working with a soldering iron).
Building firms are increasing the pace of work at large facilities through the use of electrofitting.
In the private sector, the method is not distributed due to the high cost of the equipment. Electro-coupling devices cost about 80 - 100 thousand rubles.
Cold welding
A special glue is used for this method, which is capable of softening the upper layer of the PP.
Instruction:
- Before the work starts, the parts are adjusted to the size, they acquire a set of fittings.
- Two surfaces (which are going to be connected) are degreased.
- Adhesives are applied to both surfaces.
- Elements are inserted into each other and tightly fixed for 20 seconds.
- Within an hour, the elements should not be shifted.
After one hour, the joint will reach its maximum strength, comparable to soldering, and the pipeline can be used.
Cold welding method
Glued seams can not be heated. The method is only valid for cold water pipes!
How to solder polypropylene pipes
So, having understood the available methods, most masters stop by soldering with a hand-held device. Consider in more detail the fineness of the installation. What you need to buy.
Tools and materials
- Soldering iron. Its power is selected by the diameter of the pipeline (the diameter is multiplied by 10). So, for 32 mm, you need a 320 W instrument.
- For pipes up to 40 mm suitable hand soldering iron. Over 40 mm, it is better to use instruments with centering devices.
- Set of baits. These are heating elements with Teflon coating of various diameters from 16 to 40 mm (hand-held device).
- Keys for fixing attachments.
- Pipe Roller Cutter.
- A knife for removing jags.
- Marker.
- Roulette.
- Alcohol or acetone for pre-degreasing.
- A piece of tarpaulin or a wooden scraper to clean the nozzles.
Many people are attracted by the organization of the heating system from polypropylene because of the low cost of pipes. can do everyone, you just need to know the basic rules of installation.
Types of pipes for heating and their characteristics are presented in the review.
In order to properly select PP-pipes, you need to know what characteristics should be paid attention. Here everything is about the characteristics of PP pipes and the features of choice.
Table of welding parameters and time
This is a reference table of time for which you need to fix the elements for heating and cooling after soldering. It is necessary to know that the temperature around can influence the setting time (the table gives the data for the temperature of +20 ° C).
At what temperature should polypropylene pipes be soldered? Work with PP in the cold can not. Even if the installation is done in winter in an unheated room, care should be taken to create a heat zone at the work site (the heat gun or infrared heater will cope with the task).
Table of technical parameters of soldering PP for 260 ° С
The diameter of the pipe is external (mm). | Depth of embankment (mm.) | Heating time (sec.) | Fixing time (seconds) | Time of full cooling (min.) |
16 | 12 | 5 | 4 | 2 |
20 | 14 | 6 | 4 | 2 – 3 |
25 | 16 | 7 | 4 | 3 |
32 | 18 | 8 | 4 - 6 | 4 |
40 | 20 | 12 | 6 | 4 |
50 | 23 | 18 | 6 | 4 |
63 | 26 | 24 | 6 - 8 | 5 - 6 |
Gradually a skill is developed, or a flair for how much to withstand heating. To practice, it is advised, together with a set of "clean" pipeline, to purchase polypropylene cuttings, which are usually discounted.
Step-by-step instruction
So, let's consider how soldering of pipes from polypropylene is carried out:
- The circuit is made, the details are cut off, the pipe and fitting are selected so that they fit tightly into each other without backlash.
- Marked the depth of the entrance (marker) so that there is a gap of 1 mm (not more!)
- A pair of nozzles is selected, the free entry of pipe elements into them is checked. Teflon is degreased, the nozzles are fixed in a soldering iron.
- Degrease the surface of the pipe and fitting.
- The soldering iron is installed on a flat surface, is connected to the network.
- The table determines how many seconds the heating and fixing will take place.
- The required temperature (260 ° C) is set on the thermostat.
- After the thermostat stops heating the soldering iron, you can insert the PP elements into the nozzles: first the fitting (it is thicker, warms slightly longer), then the pipe.
- The pipe is first removed, then the fitting and parts are inserted one into one before marker markings. You need to do this smoothly, you can not twist the elements! Also, do not press too hard, otherwise there may be plastic rollers that will interfere with normal circulation.
- The required seconds are maintained (from the "Fixing time" table). Then the parts are left alone for the minutes indicated in the table, as "Time of complete cooling".
- While Teflon surfaces of nozzles have not cooled down, they carefully wipe a canvas or wooden scraper, clearing of the rests of polypropylene. Do this after each soldering!
Use the pipeline can be an hour after the soldering of the last element.
In case of failure, the defective area is cut out and the solder is re-made on a clean surface.
Diffusion soldering method
The quality of the seams depends on how comfortable it is for you to work. Therefore, as much detail as possible should be welded on the stand. When it comes to the elements that will have to be soldered at the location of the pipeline, the help of a partner will come in handy. And the nozzles for these jobs are more convenient to place on the extreme position of the device.
Reinforced polypropylene pipe - how to solder?
Armored pipes have improved properties and are most often used for heating. There are:
- Fiberglass.
- Aluminum.
Installation of the first does not differ from ordinary pipes (see instructions above), therefore these pipes can be called the best option.
However, aluminum reinforcement has its own characteristics. The aluminum layer should never be in contact with the liquid, otherwise it collapses, and the sense of acquiring more expensive pipes is lost. Small misalignments inside, at the junction, can not be seen with the eye, but they can become the weak point of the system and let water pass to the metal.
To prevent this from happening, the reinforced layer is cleaned (it is necessary to do this both with pipes with a surface layer of foil, and with a middle layer of aluminum).
To remove the layer you need a small device - a shaver (usually not included in the kit of the soldering iron).
The end that needs to be cleaned is inserted into the shaver, and scrolls the same way as the pencil is cleared.
Then the part is placed in the soldering iron and everything is done as in the case of unreinforced PP.
If you do everything yourself, do not neglect the cleaning of the aluminum layer! But if the installation is performed by hired workers, it is important to follow whether the instruction was followed by the instruction is difficult (after all, without pipe stripping they still weld together). In order not to worry about the "human factor", it is better to buy fiberglass reinforced pipes!
That's basically all you need to know about polypropylene soldering. The main thing is not to rush, do not forget to clean the nozzles and avoid distortions. Manufacturers say that such seams will last for a quarter of a century.
PP pipes are good in that they are not afraid of corrosion, and also deposits do not settle inside them. In addition, it attracts the cost of products. Comparison and selection of the best option.
Which material of pipes for ventilation in a private house is preferable, you will learn in the article. Metal, plastic, and sewer pipes as ventilation.
Greetings, dear reader!
Spring has come and the season of construction and repair works is approaching. And for someone, it happens that it does not end all the year round. Today I would like to talk with you about how you can do it yourself, having the necessary tools and small skills available, to solder the plastic pipes with your own hands for heating your house, apartment or garage.
Today, this material is one of the most common elements in heating systems, easily accessible in the markets, and the soldering of heating pipes by oneself does not represent anything, absolutely nothing complicated and can be carried out by anyone, even who has never faced this before. To do this, you just need to be guided by certain rules and techniques and everything will be fine! So, now I'll tell you everything in order.
I will not dwell on the technical characteristics of polypropylene pipes, their density and composition, but briefly I want to give you examples of what advantages they have.
This is great strength and durability. But here it is important to pay special attention to what kind of pipe model you choose for your heating. The fact is that there are models that are designed, for example, only for cold water supply systems, there are those that are used for "warm floor" systems, and, of course, such as for the supply of hot coolants in the system.
- Plastic pipes are not exposed to corrosive processes.
- Flowing through them, the water makes much more noise.
- When connecting by soldering individual elements of the piping system from polypropylene, a reliable and integral connection is formed.
- Soldering of pipes is carried out without much effort by means of a special soldering iron - a simple device as such and simple to handle.
- There are no accumulations of deposits on the internal surfaces.
- The walls of polypropylene pipes do not let oxygen pass, which in turn protects metal parts from the appearance of oxide and corrosion.
- Due to the property of plasticity, it is possible to perform bends in the required places.
- And, of course, this material is environmentally friendly and can be bought in stores, as the prices are affordable and affordable, and they also weigh a little.
Next, let's consider with you which parts or parts of polypropylene will constitute a heating system that will be susceptible to soldering. When constructing a heating system using plastic pipes, such connecting elements will be needed that will facilitate our task, namely: they will allow to direct the pipes in the other direction, deploy them, move from one diameter to another, make a branch, switch to a threaded connection and the like.
Among such connecting elements are the following:
- couplings - to connect and solder pieces of pipe of equal diameter;
- adapters - to connect and solder segments of different diameter pipes;
- couplings with external thread or internal - will be useful in case of switching to a threaded connection;
- bends 450 and 900 - designed to rotate the polypropylene pipe the appropriate angle;
- bends nipple for 450 and 900 - are used when it is necessary to turn to the same degree when the diameter is changed;
- tees - for mounting three pipes in one unit;
- crossings - apply for the same purpose, but for four;
- tee, with both internal and external thread - for soldering pipes with thread to connect the third;
- connector connectors - for the mechanism of a detachable connection;
- bushings and plugs - to bring the pipeline to the "closed" position;
- various clamps (plastic, metal with rubber liners) or tile mounting - to fix the pipes to vertical surfaces, for example, walls or structures during installation;
- shutoff valves in the form of ball valves.
Now let's talk about what tools we will need, with which it will be necessary to collect all this into one single system.
- Well, firstly, it's directly the soldering iron itself or a special "welding machine" with a set of nozzles that come with it in the kit, provided for different pipe diameters.
- Next, we will need a special scissors, or a so-called cutter, for cutting the tubes you need. But if it does not, then it will be possible to use either a saw blade with a metal file, or you can use a Bulgarian. But with the help of special scissors, everything will be much easier.
- Shaver is a tool for removing aluminum foil that is inside aluminum foil reinforced polyethylene pipes, unless of course you use it.
- In order to directly fix the polypropylene material on the walls you will also need a drill and a perforator to drill holes for the holders.
- You will need a marker for thin alcohol or a simple pencil for marking the length, as well as a tape measure.
- Building level.
- Adjustable wrench.
- The pipes themselves and the connecting elements.
Now, knowing that for us all this process is necessary, and the whole instrument is prepared, the heating system is schematically shown in our picture, we proceed directly to work, which should be performed sequentially step by step. Using a marker, roulette and special scissors we measure and cut off the pipe of the sizes we need, we clean the edge from the butt, removing the chamfer and all the burrs. Then we select the adapter or connecting element we need.
Next, we check the prepared for the soldering elements for the absence of any defects. We check that the pipe is tight and completely enters the connecting element without backlashes and distortions. The surfaces to be bonded must be treated with a degreasing liquid and be sure that these parts are absolutely clean and dry.
At the edge of the tube markers mark the edge of the entrance to the connecting element. In this case, take into account the need for a gap of about 1 mm, which is necessary so that the inner diameter of the pipe does not narrow due to the displacement of its end edge inside the soldering process.
Then we prepare a soldering iron for work. We select a pair of bows we need: a sleeve (used for heating and reflowing the pipe), and a mandrel (realizes the same operations with the inner surface of couplings and fittings). Also we clean them and degrease them, fasten them to the soldering iron. We turn on the soldering iron into the network and put the temperature we need on it (we heat it to 260-300 degrees).
Now, after heating the soldering iron to the required temperature, it automatically turns off the thermostat. We take polypropylene parts for the connection and insert them into the nozzles for a few seconds.
It happens that the parts are difficult to get into the nozzles, just do a little rotation on the axis. And at first the connecting element is put on the inner nozzle, and only then the end of the pipe is inserted into the outer nozzle. When heated - remove them in the reverse order. And this is necessary because the connecting part has a larger wall thickness and therefore longer heating is required.
After the necessary warm-up, the parts are extracted from the tips of the soldering iron, smoothly and evenly inserted into each other until the marks that you previously marked with a marker match. At the same time, remember that during the hardening of parts, they can not be rotated and twisted!
After the final connection, hold the parts in a fixed position for a few seconds. Complete with soldering irons there is an instruction in which there is usually a table of soldering parameters, where the holding time for certain details is indicated.
If something suddenly happened somewhere crooked and with defects, then this piece of pipe is dismantled and a new soldering of the parts is carried out. A ready pipeline can be started in an hour.
As you have noticed, soldering pipes from polypropylene is quite simple and easy, if you do not neglect the above recommendations.
Leave your comments and subscribe to receive new articles.
On this I say goodbye to you. Take care of yourself and your loved ones. Until next time.
At the first experience of soldering with the hands of polypropylene pipes, a beginner master will inevitably have many questions that will help to remove an intelligent video
When we undertake to install the heating system or its fragments on our own, we are faced with the question of how to correctly combine the various parts among themselves. For example, two polypropylene (metal-plastic) pipes. It would seem that the task is not so fantastic. But it requires a certain skill. Therefore, the masters say, try, training will somehow bear fruit. It may be necessary at first to spend not only more time, but also some amount of material to spoil. But experience will come - that very son of the mistakes difficult.
First, buy a few clutches and corners, you can cheaper, and pipes. By the way, buy fittings of the same brand, what are you going to solder the water pipe, products of different manufacturers behave a little differently, some softer, some, on the contrary, more rigid.
Which tool
For soldering polypropylene pipes with your own hands you will need some equipment and tools:
- Special electric welding machine for soldering pipes, soldering nozzles of the required diameter, for room wiring most often use a diameter of 20.
Electric welding machine for soldering pipes
- A special device (called "sweep"), used for the processing of clean polypropylene pipes with a layer of metal "staffs";
- hacksaw / shears for cutting polypropylene;
measuring instruments (measuring tape); - A marker (or just a pencil).
How to solder a water pipe from polypropylene pipes
When soldering, watch closely the soldering points of pipes and fittings to keep them clean, dust, dirt or water may leak. If not immediately, then later.
1. Measure and cut the required length of the pipe. On the pipe there may be burrs, you can clean them with a stationery knife. If the pipe is "staffed," then we remove the metallized part with a special sweep. With the metalized pipe treated in this way, we work in the same way as with a polypropylene pipe.
2.If soldering an ordinary water pipe, it is advisable not yet to prilovchishsya mark pencil on the pipe at what depth the pipe is soldered into the fitting, tee or muff, and if you use the pipe "staff", then using the stripping you have the size that is needed for connections with fittings; The sweep is adjusted to the soldering size.
Of course, you will learn a lot by the empirical method itself, but from the intelligent advice of the masters, something that has already passed in this matter should not be abandoned. We offer you some good video materials that will be of considerable practical use to you.
How to solder pipes in the home
Not quite the standard method
Below is one of the atypical ways, non-standard soldering of polypropylene, this option is used among other professionals